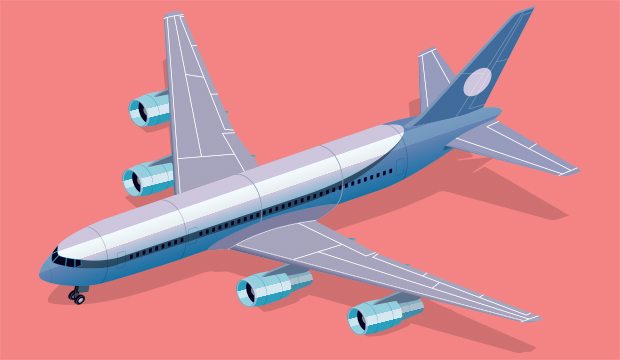
Aerospace Applications
Rising fuel costs, environmental regulations and an increase in airline traffic have helped drive the increasing use of composite materials in the aerospace industry. Composites are used in military, business and commercial aircraft of all sizes, including spacecraft.
NASA and Boeing Build and Test All-Composite Cryogenic Tank
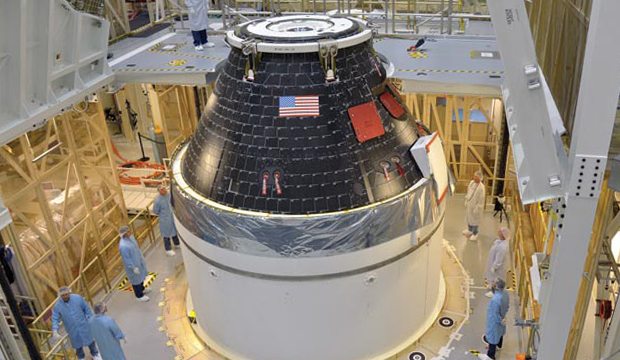
- Application: Cryogenic tanks
- Scope: 5.5-meter diameter CFRP cryotanks
- Year Introduced: 2013
- Volume: Ongoing demonstration projects
- Manufacturing Process: Out-of-autoclave manufacturing
CFRP cryotanks will allow astronauts to fly to Mars and beyond
With budgets tight, NASA is looking for every opportunity to reduce the cost of launching people and payloads into space. New cryogenic rocket tanks made entirely of composite materials could provide a real cost-saving opportunity.
The space agency uses the “cryotank” rocket fuel tanks to contain liquid hydrogen or liquid oxygen fuels at cryogenic temperatures (below -238 F). The high-energy propellant in the tank is required for extended human exploration missions beyond low-Earth orbit.
In the past, cryotanks have been made with metals or with metal-lined composite materials. But NASA and Boeing have now successfully built and tested an all-composite, CFRP 5.5-meter diameter tank. Their research was part of the Composite Cryogenic Technology Demonstration Project.
The composite cryotank is one of the largest and lightest cryogenic liquid hydrogen fuel tanks ever manufactured. It is also a step toward a planned 8.4-meter tank that could reduce the weight of rocket tanks by 30 percent and cut launch costs by at least 25 percent.
NASA spends more than $10,000 to put a pound of material into Earth orbit, and any weight saved on the cryotanks can be used for payload instead. But the lightweight CFRP material used for the tank must also be strong enough to withstand the harsh conditions of space.
Composites manufacturers are very familiar with making products that save on weight and cost without sacrificing performance. Manufacturing an all-composite cryotank was a challenge, however, since engineers could not rely on past design or production data. “A lot goes into the design of the materials and the manufacturing to make sure that [the tank] is durable enough to withstand the cryogenic environments,” says John Vickers, the cryotank project manager at NASA. The space agency was willing to move into this uncharted territory because of the potential lightweighting and cost-cutting benefits.
The Boeing/NASA team will use an out-of-autoclave (OOA) manufacturing process to produce the 8.4-meter tank because no autoclave mold is large enough to produce a one-piece cryotank of that size.
NASA plans to use the composite cryogenic tank to power the upper stage of the rocket engine for NASA’s Space Launch System. This new rocket system will take humans to Mars and on other deep space exploration missions.