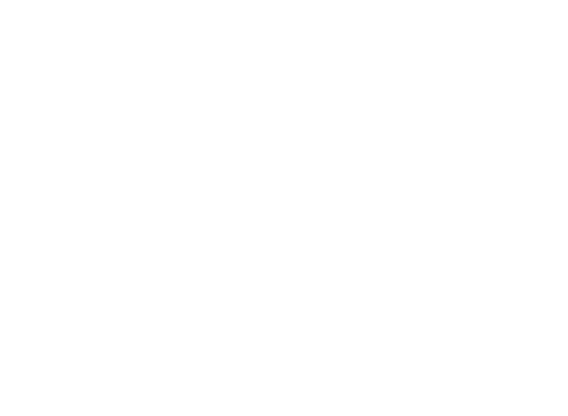
History Of Composites
Composites have played an important role throughout human history, from housing early civilizations to enabling future innovations. No matter the year, composites make the world a better place.
Ancient Times
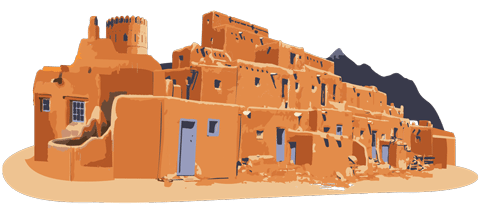
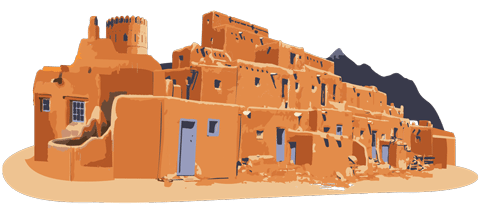
One of the earliest uses of composite material was by the ancient Mesopotamians around 3400 B.C., when they glued wood strips at different angles to create plywood. The concept of “composite” building construction has existed since ancient times. Civilizations throughout the world have used basic elements of their surrounding environment in the fabrication of dwellings including mud/straw and wood/clay. “Bricks” were and still are made from mud and straw.
In the 12th century A.D., Mongol warriors used composite materials (bamboo, silk, cattle tendons and horns, and pine resin) to craft archery bows that were swifter and more powerful than those of their rivals: They put the tendons on the tension (outer) side and sheets of horn on the compression (inner) side of the bow over a core of bamboo. They tightly wrapped the structure with silk and sealed it with pine resin. A museum tested some of the surviving bows, now more than 900 years old, and found that the old bows were nearly as strong as modern ones—and could hit targets as far away as 490 yards (the length of nearly five football fields).

Polymer Resins

In the late 1800s, canoe builders began experimenting with different materials to make paper laminates. They tried gluing layers of kraft paper (sturdy, machine-made paper created from wood pulp) together with shellac. It was a good idea but ultimately flopped because the available materials were not up to the task. The first synthetic (man-made) resins that could be converted from liquid to solid (using a chemical process called polymerization) were developed between 1870 and 1890. These polymer resins are transformed from the liquid state to the solid state by crosslinking the molecules.
The 1930s heralded a new era for resins – and ultimately the composites industry as a whole. Unsaturated polyester resins were patented in 1936 by Carleton Ellis. Because of their curing (or hardening) properties, they became the primary choice for resins in composites manufacturing. By the late 1930s, other high-performance resin systems had become available, including epoxy resins.
A New Era
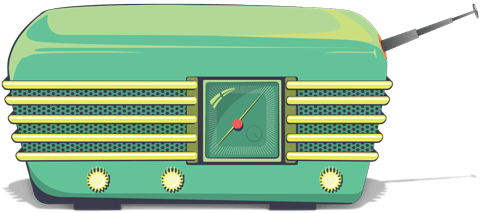
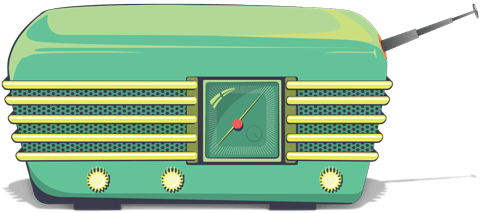
Belgian-born U.S. chemist Leo Hendrik Baekeland ushered in the modern era of composites in 1907 with his creation of Bakelite, one of the first synthetic resins. The resin was extremely brittle, but Baekeland found he could soften and strengthen it by combining it with cellulose. The first commercial use of Bakelite was to make gearshift knobs in 1917 for Rolls Royce automobiles. New and better resins were produced during the 1920s and 1930s. In the early 1930s, two U.S. chemical companies, American Cyanamid and DuPont, further developed polymer resins. In the course of their experimentation, both companies independently formulated polyester resin for the first time.
In the late 1930s, the Owens-Illinois Glass Company developed a process for drawing glass into thin strands or fibers and began weaving them into a textile fabric. These new glass fibers, combined with newer synthetic (polyester) resins, produced strong and lightweight composites. In 1942, engineer Ray Greene of Toledo, Ohio (who had worked for the Owens-Illinois Glass Company) made a dinghy from fiberglass and polyester resin. The boating world would never be the same.
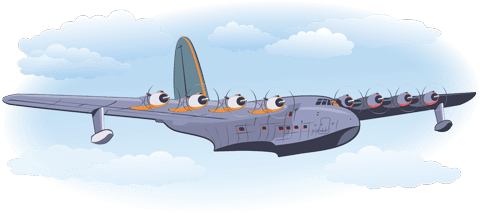
A Growing Industry
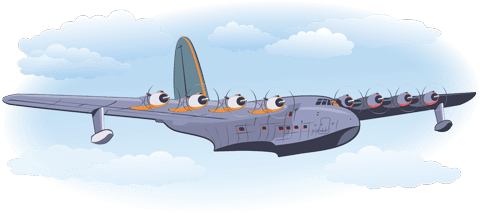
Howard Hughes used composite wing spars (thin wood layers and plastic resin) on the Spruce Goose. The fledgling composites industry further developed during World War II as the military searched for materials to cut the weight of air and water craft while, at the same time, increasing their strength, durability and resistance to weather conditions and the corrosive effects of salt air and water. By 1945, over seven million pounds of fiberglass were used, primarily for military applications. Soon the benefits of FRP composites, especially its corrosion resistance became known to the public sector. Fiberglass pipe, for instance, was first introduced in 1948 for what has become one of its widest areas of use within the corrosion market, the oil industry.
Composites continued to take off after the war and grew rapidly through the 1950s: Boats, trucks, sports cars, storage tanks, pipes, ducts and many other products were built using composites. In 1953, the 1st production Chevrolet Corvette with fiberglass body panels rolled off the assembly line. Also in the early 1950s, manufacturing methods such as pultrusion, vacuum bag molding, and large-scale filament winding were developed. Filament winding became the basis for the large-scale rocket motors that propelled exploration of space in the 1960’s and beyond.
Widespread Use
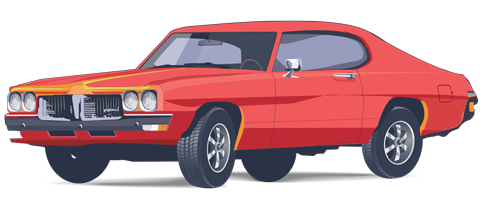
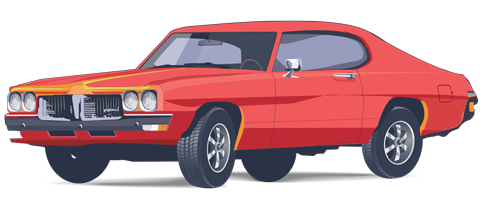
Although the first carbon fiber was patented in 1961, it took several more years for carbon fiber composites to become commercially available. The use of carbon fiber helped advance many applications in a number of industries, including aerospace, automotive, marine and consumer goods. In 1966, Stephanie Kwolek, a DuPont chemist, invented Kevlar, a para-aramid fiber that is strong enough to be used in advanced composites; Kevlar is best known for its use in ballistic and stab-resistant body armor. New and improved resins helped grow the demand for composites, particularly for use in higher temperature ranges and corrosive applications. In the 1970s, the automotive market surpassed marine as the number one composites market – a position it retains today.
During the late 1970’s and early 1980’s, composites were first used in a number infrastructure applications in Europe and Asia, including the world’s first highway bridge using composites reinforcing tendons and the first all-composites bridge deck. The 1990’s saw the first all-composites pedestrian bridge installed in Aberfeldy, Scotland; the first FRP reinforced concrete bridge deck built in McKinleyville, West Virginia; and the first all-composites vehicular bridge deck in Russell, Kansas. Numerous FRP composites pedestrian bridges have been installed in U.S. state and national parks in remote locations not accessible by heavy construction equipment, or for spanning over roadways and railways.
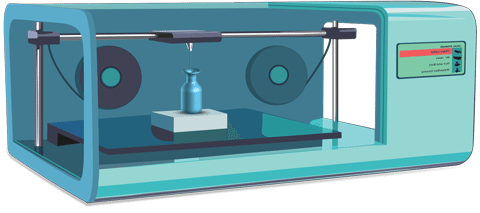
Modern Day
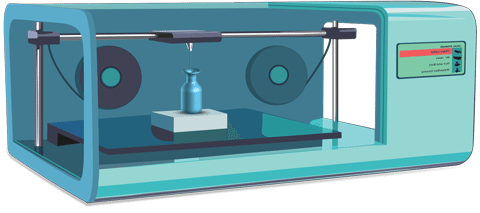
Many industrial designers and engineers now specify composites for various components within industries such as manufacturing, construction and transportation. FRP composites systems are used in thousands of installations around the world to strengthen or seismically upgrade reinforced concrete or masonry structures ranging from buildings and parking garages to transportation structures such as bridge columns and decks. In the early 2000s, nanotechnology began to be used in commercial products. Composites play an important role in carbon nanotubes; bulk carbon nanotubes can be used as composite fibers in polymers to improve the mechanical, thermal and electrical properties of the bulk product. Nano-materials are incorporated into improved fibers and resins used in new composites.
The rise of 3-D printing in the 2010s brought manufacturing into homes and small businesses, allowing users to bring to life on a desktop any item they can dream up with a CAD program. Composites companies are jumping into the field by 3-D printing items with reinforced fibers. Discontinuous strands of carbon fiber or fiberglass are most frequently used to reinforce plastics in 3-D printing processes across every market sector, including automotive, aerospace, tooling, medicine and infrastructure. These reinforcements deliver the strength of composites with less material in less time and can be designed and prototyped from one desktop. In 2014, MarkForged announced the world’s first carbon fiber 3-D printer.
Looking Ahead
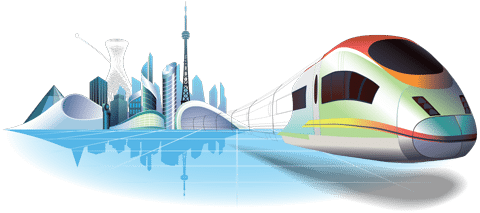
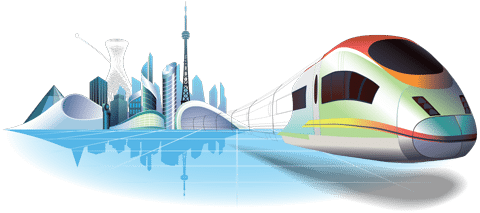
The composites industry continues to evolve. The use of FRP composites has already transformed the marine, automotive and aerospace markets. Many specific applications in infrastructure and chemical processing have seen similar dramatic conversions. There is huge potential for a similar technology shift in the architectural and building & construction segments as the industry takes advantage of the design flexibility, durability, low weight, corrosion resistance, and other properties that composites offer.
In 2015, the US Department of Energy announced the Institute for Advanced Composites Manufacturing Innovation, a $259 million public-private partnership. The Institute will focus on making advanced composites less expensive and less energy-intensive to manufacture, while also making composites easier to recycle. The development of new fibers and resins will help create even more applications for composites. Environmentally friendly resins will incorporate recycled plastics and bio-based polymers as composites feed the demand for stronger, lighter and environmentally friendly products. Composites will continue to make the world a better place.