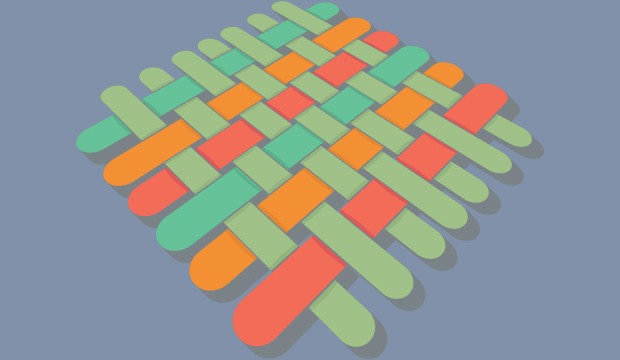
Composites
vs.
Steel
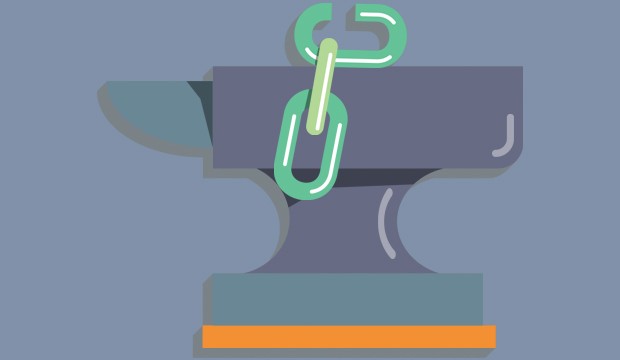
Steel holds an iconic place in America, from images of skyscrapers soaring into the clouds to Superman bending a steel beam. It is one of the most frequently used metals in the world. But it faces stiff competition from composites, which are increasingly replacing steel in applications ranging from car parts to bridge decks.
Composites offer several advantages over steel, which has intrinsic design limitations, is heavy and costly to transport and is susceptible to corrosion, which leads to high maintenance costs. Consider these attributes:
- Composites are lighter than steel – A cubic foot of cast steel weighs approximately 490 pounds. Depending on the material formulation, composites can be up to 70 percent lighter.
- Composites are incredibly strong – They can be custom-tailored to add strength in critical areas, such as spots that may bend or wear out. With steel, if greater strength is needed in any area then more metal must be added, which in turn increases weight.
- Composites are corrosion resistant – In outdoor applications, composites stand up to severe weather and wide temperature changes. Steel rusts easily unless it is painted or coated with zinc. And corrosion is expensive, with annual direct costs hitting $2.2 trillion.
- Composites are nonconductive – By their very nature, metals like steel conduct electricity. Composites are superior insulators: They don’t respond to an electric field and resist the flow of an electric charge.
- Composites allow for parts consolidation – A single piece made of composites can replace an entire assembly of metal parts, streamlining the production process and reducing lifetime maintenance.
The advantages are clear cut. That’s why companies are making the steel-to-composites conversion for everything from manhole covers to valve covers. Now that you know the benefits, take a closer look at specific applications within architecture, automotive, infrastructure and other markets.