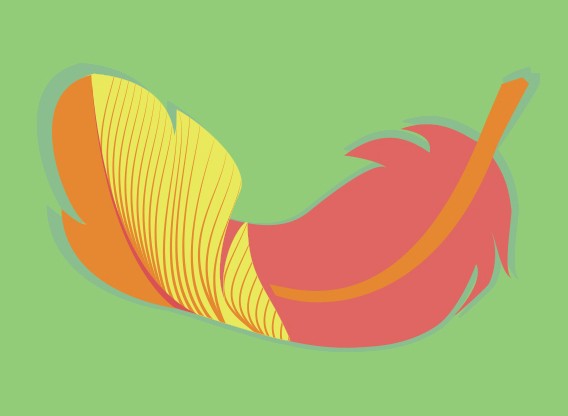
Lightweight
Composites materials are both strong and light. That’s a winning combination. Who wouldn’t want to work with a material that’s simple to ship and carry? Lightweight composites can save you money and manpower.
Fiber-reinforced composites offer excellent strength-to-weight ratios, exceeding those of other materials. For example, carbon fiber-reinforced composites are 70 percent lighter than steel and 40 percent lighter than aluminum. Producing parts that are light weight is critical to industries such as transportation, infrastructure and aerospace for a variety of reasons. Lightweight composites are easy to handle and install, can reduce costs on projects and help ensure adherence to regulations and standards.
Easy Installations
One of the top advantages of using lightweight composites is that they are simple to handle, transport and install. This saves time on projects. Wolf Trap National Park in Virginia installed a pedestrian bridge with FRP decks in 2012. The bridge was 80 percent lighter than a concrete one, making it faster to lift, move and place by crane. The deck was installed in three days, while a concrete one would’ve taken at least four weeks. Lightweight composites also simplify installations in remote locations, such as utility poles in marshlands or pipelines on mountains.
Reduced Costs
Lighter parts and products often save money. And saving on weight and cost is music to the ears of many end users. NASA and Boeing recently tested an all-composite cryogenic tank used to carry fuel on deep space missions. The tank, one of the largest and lightest ever manufactured, is the latest step toward the planned 8.4-meter tank that could reduce the weight of rocket tanks by 30 percent and cut launch costs by at least 25 percent.
Adherence to Standards
Composites are often the answer when applications need to meet specific standards and regulations. The most notable example relates to fuel efficiency. Within the automotive industry, meeting Corporate Average Fuel Efficiency (CAFE) standards of 36.6 mpg by 2017 and 54.5 mpg by 2025 provides impetus for using lightweight materials. Major OEMs have optimistic plans – often involving composites – to drastically reduce the gross weight of vehicles. In 2013, GM introduced the Chevrolet Silverado Cheyenne concept vehicle featuring some carbon fiber-reinforced parts. It’s approximately 200 pounds lighter than the base curb weight of the 5.3L Silverado. Volkswagen created the Transporter, a utility concept truck weighing just 3.5 tons. It saves on diesel consumption and carbon dioxide emissions by providing 40 percent more payload and up to 30 percent savings in shipments.