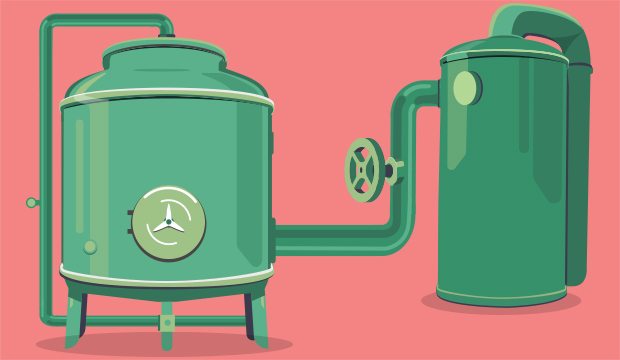
Pipe & Tank Applications
FRP pipe and tank installations are on the rise – above and below ground, in commercial, municipal and residential applications. Low-cost natural gas leads to the development of new chemical facilities and the expansion of older ones for chemical processing. That, in turn, creates demand for FRP pipes.
Daniel Company Uses GFRP in Odor-Removing Plant Filters
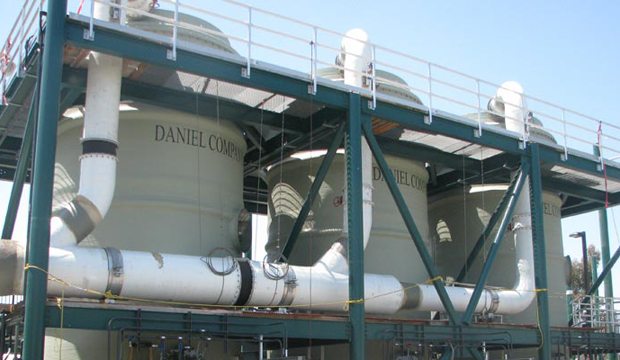
- Application: Biotrickling filters for wastewater and sewage treatment plants
- Scope: GFRP ductwork, tanks and dampers
- Volume: Customized systems for several U.S. plant sites
- Process: Filament winding, random chop and hand lay-up
Biological air scrubbers break down chemical compounds to mitigate unpleasant odors
The odors that emanate from water and sewage treatment plants make them unpopular neighbors. But Daniel Company, based in California, is designing and manufacturing biotrickling filters (BTFs) that remove most of the odor from the plants’ discharges in an environmentally friendly way.
At the heart of a BTF system is the Thiobacillus bacterium that feeds on the hydrogen sulfide and other compounds that the plant produces during treatment. The bio-organism breaks down these smelly compounds, eliminating the odor and leaving very few byproducts. Glass fiber reinforced polymer (GFRP) vessels filled with a special medium provide a habitat where the Thiobacillus bacterium can thrive. Daniel Company uses GFRP for these systems because of the material’s high resistance to corrosion.
A BTF includes ductwork, tanks and dampers custom designed by Daniel Company for each specific plant site. Ashland Chemicals, which has helped Daniel Company develop the BTF process, supplies the epoxy vinyl ester resins for GFRP production. Manufacturing is extremely labor intensive, and the techniques used for the various BTF components vary. Daniel Company uses filament winding processes for cylinders and random chop and hand lay-up processes for rectangular structures.
European treatment plants have been using BTFs for years, but the U.S. has preferred chemical reagents because they were relatively inexpensive here. BTFs have gained traction in North America, however, as environmental regulations become more stringent and communities demand more eco-friendly practices in treatment plants.
Daniel Company’s largest BTF installation to date is in Orange County, Calif. It has 16 biotrickling filters that stand 42 feet tall and measure 10 feet in diameter. This plant has reduced its use of chemicals by 90 percent. The BTFs are also good at getting the smells out; one installation in Lubbock, Texas, had a 99 percent efficiency in removing hydrogen sulfide from the plant’s emissions.