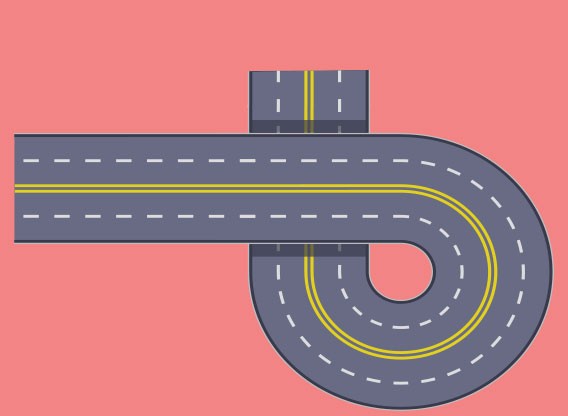
Infrastructure Applications
Composites have a long history of use throughout the infrastructure industry. They are often utilized as reinforcing materials in repair and retrofitting of existing infrastructure applications. Composites also are the material of choice for corrosion-resistant pipes and tanks. And more bridge decks are now made from FRP than ever before.
Composites Carry an Electric Load
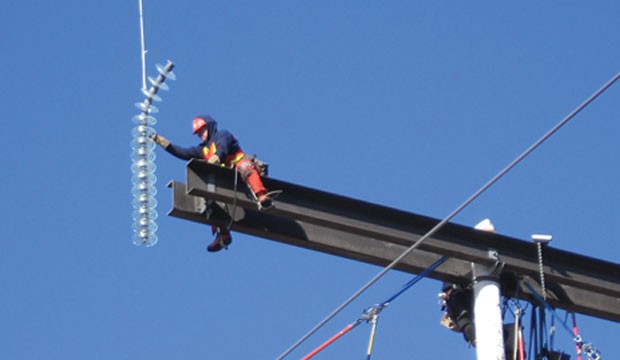
- Application: Utility transmission crossarms
- Project Scope: 1,000 GFRP crossarms
- Manufacturing Process: High-pressure Injection Molding
- Installation: 2015
- Location: British Columbia, Canada
Custom GFRP architecture allows utility crossarms to withstand winds and ice
Nearly a decade ago, BC Hydro, an electric utility serving British Columbia saw that its transmission line stretching across 40 rugged miles along the northwest coast was nearing the end of its useful life. The wooden crossarms supporting the conductors that transmit electricity were beginning to rot. Furthermore, the utility realized it needed a better option to carry the additional electricity required for the region’s growing industry.
BC Hydro approached Transmission Innovations Inc. in Vancouver, Canada, which proposed a GFRP transmission crossarm capable of carrying up to half a million volts. After performing finite element analysis to prove that the product would support the needs of the new line, Transmission Innovations contracted with Creative Pultrusions Inc., an Alum Bank, Pa.-based manufacturer of FRP composite profiles, to create 24 46-foot long samples for testing at Power Tech Laboratories. The products underwent more than five years of laboratory and real-life applications before approval was given.
The final product, now being installed in the Canadian mountains, features a 6 x 14 x ½-inch C-channel shape for each transmission arm, which range from 46 to 50 feet long. The crossarms utilize a custom fiber architecture designed by engineers from Transmission Innovations and Creative Pultrusions. “It incorporates a lot of glass fiber stitched fabrics, roving and continuous filament mat, but the big difference is it’s made out of a polyurethane matrix,” says Dustin Troutman, director of marketing and product development for Creative Pultrusions.
Polyurethane resins are well suited for applications with extraordinary requirements for robustness, impact strength and longevity. Those characteristics are needed for a transmission line that must resist high wind and ice loads and the possibility of critical stress should a component break. “The polyurethane is a very forgiving resin in terms of its ability to help distribute stresses,” Troutman explains. “It drastically increases the interlaminar shear strength, which increases the bond strength between the layers of mat and roving – and it’s very, very tough.”
The polyurethane profile is reinforced with E-glass and features a polyester surfacing veil to give it added protection from the fiber blooming that can result from long-term UV exposure. Creative Pultrusions used high-pressure resin injection in the pultrusion process to push the polyurethane resin into the glass reinforcements through a series of custom dies.
Troutman expects the crossarms to last 75-plus years, unlike their wooden counterparts. “In areas that are swampy or have high moisture, wood degrades relatively fast,” he says. “Wood has a tendency to rot, so utility poles and crossarms in those types of environments may only last 20 years.”
The performance of composites will be put to the test as up to 1,000 GFRP crossarms will be installed on existing poles in one of the world’s largest temperate rainforests, the Great Bear Rainforest between Vancouver and southeast Alaska.