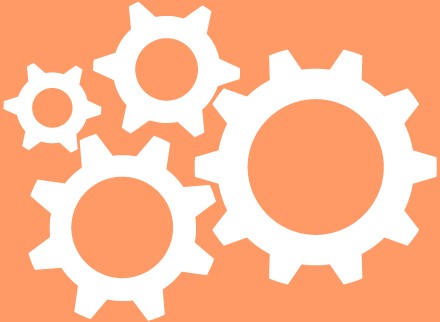
Resin Transfer Molding
Resin transfer molding (RTM) is an intermediate volume molding process for producing composites. In RTM, resin is injected under pressure into a mold cavity. This process produces parts with two finished surfaces.
By laying up reinforcement material dry inside the mold, any combination of material and orientation can be used, including 3-D reinforcements. Part thickness is determined by the tool cavity. Fast cycle times can be achieved in temperature-controlled tooling and the process can range from simple to highly automated. RTM can use a wide variety of tooling, ranging from low-cost composite molds to temperature controlled metal tooling. Vacuum assist can be used to enhance resin flow in the mold cavity.
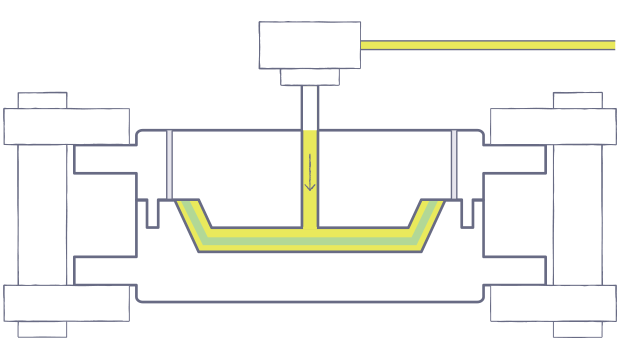
Process:
The mold is gel coated conventionally, if required. The reinforcement (and core material) is positioned in the mold and the mold is closed and clamped. The resin is injected under pressure, using mix/meter injection equipment, and the part is cured in the mold. The reinforcement can be either a preform or a pattern cut roll stock material. A preform is a reinforcement that is formed to a specific shape in a separate process and can be quickly positioned in the mold. RTM can be done at room temperature; however, heated molds are required to achieve fast cycle times and product consistency. Clamping can be accomplished with perimeter clamping or press clamping.
Molds:
RTM can utilize either hard or soft tooling depending upon the expected duration of the run. Soft tooling would be either polyester or epoxy molds, while hard tooling may consist of cast machined aluminum, electroformed nickel shell, or machined steel molds. RTM can take advantage of the broadest range of tooling of any composites process. Tooling can range from very low-cost to high-cost, life-long molds.