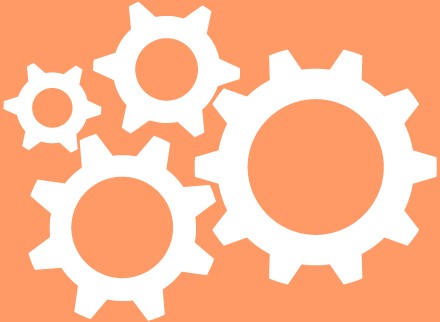
Compression Molding
Compression molding is a high-volume, high-pressure method suitable for molding complex, fiberglass-reinforced polymer parts on a rapid cycle time.
There are several types of compression molding that are defined by the type of material molded: sheet molding compound (SMC), bulk molding compound (BMC), thick molding compound (TMC), and wet lay-up compression molding. Compression molding tooling consists of heated metal molds mounted in large hydraulic presses. The process can be automated. Compression molding enables part design flexibility and features such as inserts, ribs, bosses and attachments. Good surface finishes are obtainable, contributing to lower part finishing cost. Subsequent trimming and machining operations are minimized in compression molding and labor costs are low.
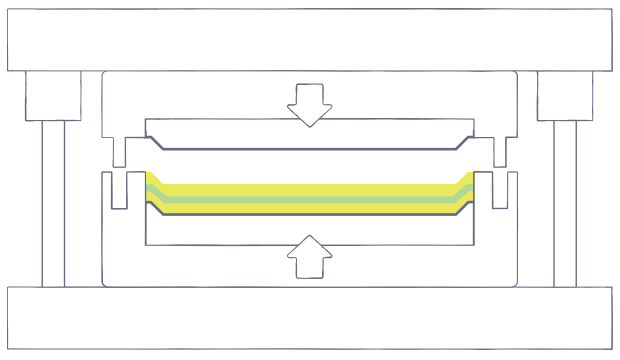
Process:
The mold set is mounted in a hydraulic or mechanical molding press and the molds are heated from 250° to 400° F. A weighed charge of molding material is placed in the open mold. The two halves of the mold are closed and pressure is applied. Depending on thickness, size, and shape of the part, curing cycles range from less than a minute to about five minutes. After cure, the mold is opened and the finished part is removed. Typical parts include automobile components, appliance housings and structural components, furniture, electrical components, and business machine housings and parts.
Molds:
Tooling usually consists of machined or cast metal or alloy molds that can be in either single or multiple-cavity configurations. Steel molds are hardened and sometimes chrome plated for enhanced durability. The molds are heated using steam, hot oil, or electricity. Side cores, provisions for inserts, and other refinements are often employed. Mold materials include cast of forged steel, cast iron, and cast aluminum. Matched metal molds can cost 50 times as much as an FRP open mold and tooling in the $50,000-$500,000 range is not uncommon.