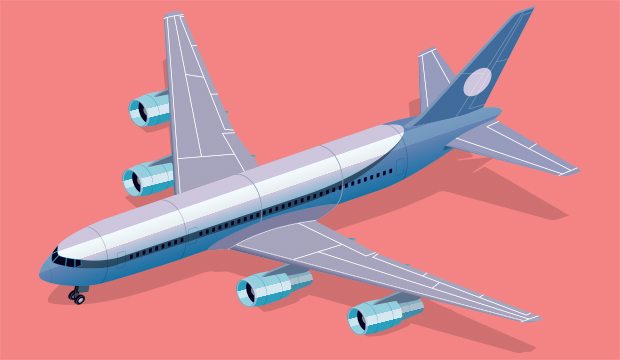
Aerospace Applications
Rising fuel costs, environmental regulations and an increase in airline traffic have helped drive the increasing use of composite materials in the aerospace industry. Composites are used in military, business and commercial aircraft of all sizes, including spacecraft.
CFRP Reinforces World’s First Single-Engine, Light-Sport Aircraft
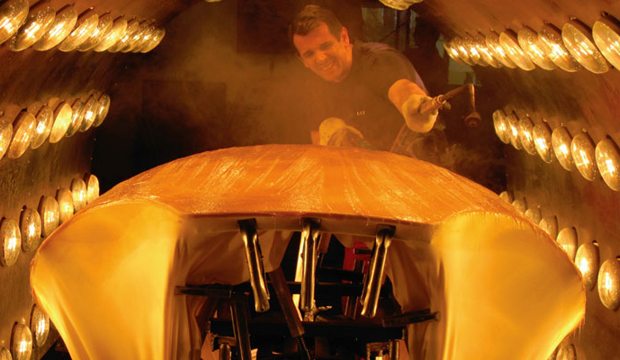
- Application: Single-engine, light-sport aircraft
- Scope: Almost all structural parts are made from CFRP
- Year Introduced: 2016
- Volume: Plans for approximately 20 aircraft per year
- Manufacturing Process: Vacuum infusion molding
CFRP aircraft combines high-performance, safety and fuel savings
An Italian start-up company is manufacturing the world’s first single-engine, light-sport aircraft composed almost entirely of carbon fiber reinforced polymer (CFRP).
NASHERO, based in San Giovanni in Croce, Italy, says that its two-seat, high-performance aircraft is designed for pilot-owners who want to travel in comfort and safety—and in an environmentally friendly way. “To us, high-performance implies extremely low fuel consumption for the distance traveled and extremely low environmental impact,” says Naresh Sharma, company CEO. The new CFRP aircraft will have significantly lower emissions than low-emission hybrid automobiles on a per-seat mile.
Composites offer several advantages over the aluminum alloys typically used in small aircraft construction. They are lower in weight and resist corrosion, but at the same time have excellent fatigue strength and stiffness. Because manufacturers can mold them into sculpted shapes, composites also offer greater design flexibility and have the potential for better aero-elastic tailoring of flying surfaces.
With its lighter, stronger overall structure, the CFRP aircraft will be able to accommodate a lighter engine and a larger payload. Plus, at least one of plane’s safety features relies on CFRP’s excellent crash absorption properties. The plane’s safety cell can take a frontal crash with minimal transfer of impact energy to the pilot or the passenger. A second safety element is an integrated aircraft ballistic parachute recovery system—essentially a parachute for the entire plane—embedded in the fuselage.
NASHERO selected a range of CFRP materials for the aircraft and developed an innovative vacuum infusion process to produce aircraft parts with the lowest possible void content in the structure. Its manufacturing process has decreased material scrap and has reduced chemical waste to below two percent (compared to some industry sector’s waste percentages of as much as 30 percent).
The only parts on the aircraft that will not be composed of CFRP are the engine mount—required by regulation to withstand temperatures of about 1000 C—and areas of the plane where a load must be transferred from one part of the structure to another. For the load transfer areas, NASHERO will embed aluminum and titanium hard points between layers of the CRFP’s reinforcement fibers.
With manufacturing, assembly and system integration of the first CFRP aircraft already well underway, NASHERO should be ready to conduct flight tests sometime in 2016. The company then plans to move to a larger building that can support production of 20 aircraft per year. At least one of these models will be constructed with less expensive fiberglass composites rather than CFRP.