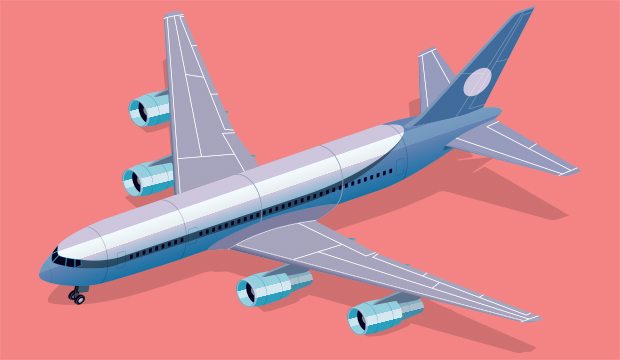
Aerospace Applications
Rising fuel costs, environmental regulations and an increase in airline traffic have helped drive the increasing use of composite materials in the aerospace industry. Composites are used in military, business and commercial aircraft of all sizes, including spacecraft.
3-D Printer Allows Astronauts to Build Tools in Space
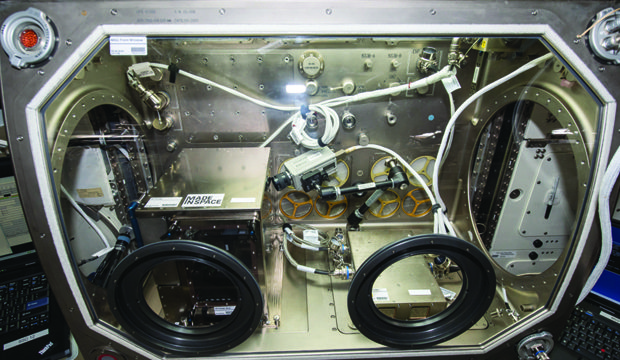
- Application: 3-D printed parts
- Scope: 21 test coupons and tools
- Year Introduced: 2014
- Volume: Prototype test unit
- Manufacturing Process: Additive manufacturing
Additive manufacturing allows astronauts to building tools in space
When Commodore Barry Wilmore misplaced a torque wrench on the International Space Station (ISS), he couldn’t run out to the nearest hardware store for a replacement. But Wilmore didn’t have to wait for the next supply rocket to bring him a new tool; he simply printed out a replacement on the ISS’s new 3-D printer.
California-based Made In Space Inc., which developed a special 3-D printing technology for space, supplied the ISS with its inaugural Zero-G Printer and sent the design file for the new part to Wilmore. The company hopes that constructing materials, tools and structures in space, rather than building them on earth, will accelerate space development.
The Zero-G Printer uses extrusion printing to layer hot, liquefied thermoplastics (specifically acrylonitrile butadiene styrene, or ABS) and produce a part. Before sending the printer into space, Made In Space flight-tested the printer on a C9 aircraft simulating a zero-gravity environment by going into freefall 400 times (20 seconds each time). After the printer successfully passed this test, NASA launched it into space in September 2014 to test the long-term effects of microgravity on the 3-D printing process.
Astronauts produced the first 3-D printed parts in space on November 24, 2014. The 21 items they printed over the next five months came back to earth in April 2015. On the surface, the parts look the same as their earth-printed counterparts, but Made In Space is performing further testing to see if any other properties have changed.
Printing tools in space makes sense since it costs $10,000 per kilogram to send something into orbit. Manufacturing the part on the space station would be much more economical, especially since it reduces the need for carrying multiple spare parts into space. Astronauts could simply print them out as needed. NASA believes that as many as 82 percent of failed parts on the ISS could be fabricated or repaired using additive manufacturing.
After successfully completing the first trial of a 3-D printer in zero gravity, Made In Space is looking forward to expanding its role in space. The company hopes to partner with other companies to manufacture complex parts, made from multiple materials, not just on the International Space Station but throughout the galaxy. Other more down-to-Earth locations—like a submarine or a research station on Antarctica—could also benefit from the company’s 3-D printing technology.