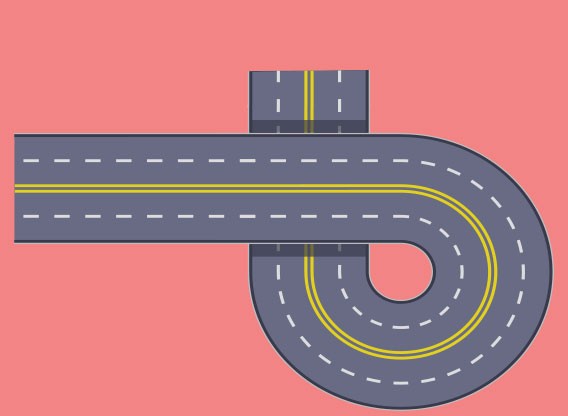
Infrastructure Applications
Composites have a long history of use throughout the infrastructure industry. They are often utilized as reinforcing materials in repair and retrofitting of existing infrastructure applications. Composites also are the material of choice for corrosion-resistant pipes and tanks. And more bridge decks are now made from FRP than ever before.
Installed Fast and Built to Last
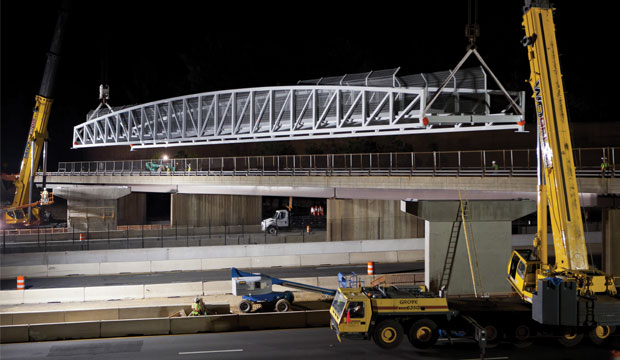
- Application: Pedestrian truss bridge
- Project Scope: 57 prefabricated deck panels
- Manufacturing Process: Vacuum Infusion Processing
- Installation: 2012
- Location: Vienna, Va.
Lightweight bridge decks allow for easy installation with little traffic disruption
Wolf Trap National Park for the Performing Arts hosts a variety of shows at its outdoor amphitheaters, ranging from jazz concerts to dance recitals. To walk from one facility to another, thousands of spectators often filed along a narrow curb over a vehicle bridge. The park put an end to this potentially dangerous situation by completing construction of a pedestrian bridge in April 2012.
The bridge, which crosses over a 10-lane highway leading to Dulles International Airport, was designed by the Federal Highway Administration (FHWA). The FHWA required accelerated construction to reduce lane closures that would hamper access to the busy airport. FRP bridge decks fabricated by Composite Advantage in Dayton, Ohio, offered the ideal solution. The deck panels were prefabricated, including the wear surface, curbs and expansion joints. This reduced on-site construction time. More importantly, the FRP bridge deck is 80 percent lighter than a concrete deck, making it faster to lift, move and place by crane.
Composite Advantage supplied 57 prefabricated deck panels measuring 15.5 x 8.3 feet. Each panel weighed only 880 pounds. The decks were manufactured using the company’s FiberSPAN™ molded sandwich construction, which employs fiberglass top and bottom skins and closely-spaced internal webs that function like a series of I-beams. The panels were assembled on three spans ranging from 138 to 170 feet long alongside the highway.
Installation took place on three consecutive nights at 1 a.m., when traffic was light. Each assembled truss – including the steel, FRP deck and fencing – was towed to its position on the adjacent vehicle bridge. Then the contractors stopped traffic and two cranes lifted the truss into place, where it was bolted down. The highway was only closed for 15 minutes each evening. For two weeks following installation, construction workers finished the detail work, such as sealing joints, completing the railing and finishing the ends of the fencing.
The contractor on the project, Shirley Contracting Company LLC, Lorton, Va., never worked with composite decks before. “We were able to install the entire deck in about three days. A traditional concrete deck, given the location, would have taken at least four weeks,” says John A. Majane III, senior structural project manager for Shirley Contracting Company. “[Another benefit] was the ability to assemble the deck off site, which reduced costs and the risk associated with working over traffic.”
Majane admits that cost is a factor when it comes to using FRP bridge decks. But he would consider composites for future projects. “This pedestrian truss bridge over traffic was a perfect application for the product,” he says.