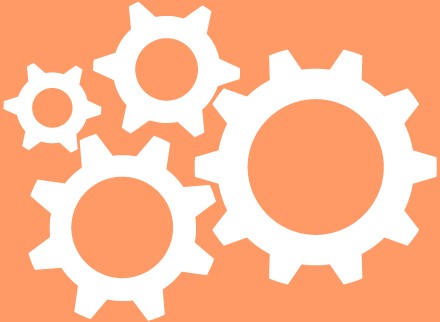
Hand Lay-Up
Hand lay-up is the most common and least expensive open-molding method because it requires the least amount of equipment. Fiber reinforcements are placed by hand in a mold and resin is applied with a brush or roller. This process is used to make both large and small items, including boats, storage tanks, tubs and showers.
Hand lay-up is an open molding method suitable for making a wide variety of composites products from very small to very large. Production volume per mold is low; however, it is feasible to produce substantial production quantities using multiple molds. Hand lay-up is the simplest composites molding method, offering low cost tooling, simple processing, and a wide range of part sizes. Design changes are readily made. There is a minimum investment in equipment. With skilled operators, good production rates and consistent quality are obtainable.
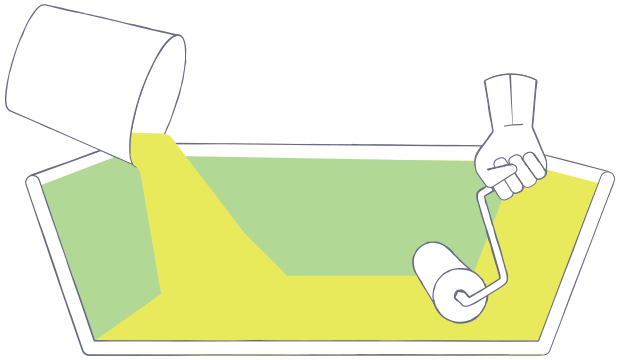
Process:
Gel coat is first applied to the mold using a spray gun for a high quality surface. When the gel coat has cured sufficiently, roll stock fiberglass reinforcement is manually placed on the mold. The laminating resin is applied by pouring, brushing, spraying, or using a paint roller. FRP rollers, paint rollers, or squeegees are used to consolidate the laminate, thoroughly wetting the reinforcement and removing entrapped air. Subsequent layers of fiberglass reinforcement are added to build laminate thickness. Low density core materials such as end-grain balsa, foam, and honeycomb, are commonly used to stiffen the laminate. This is known as sandwich construction.
Molds:
Simple, single cavity molds of fiberglass composites construction are generally used. Molds can range from small to very large and are low cost in the spectrum of composites molds.