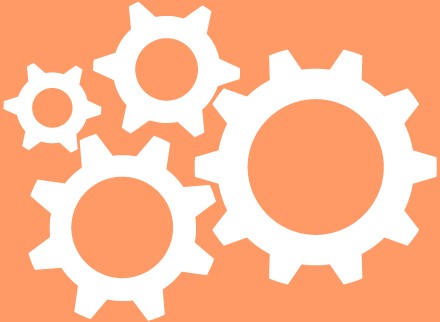
Filament Winding
Filament winding is an automated open molding process that uses a rotating mandrel as the mold. The male mold configuration produces a finished inner surface and a laminate surface on the outside diameter of the product.
Filament winding results in a high degree of fiber loading, which provides high tensile strength in the manufacture of hollow, generally cylindrical products such as chemical and fuel storage tanks, pipes, stacks, pressure vessels, and rocket motor cases. The process makes high strength-to-weight ratio laminates and provides a high degree of control over uniformity and fiber orientation. The filament winding process can be used to make structures that are highly engineered and meet strict tolerances. Because filament winding is computer-controlled and automated, the labor factor for filament winding is lower than other open molding processes.
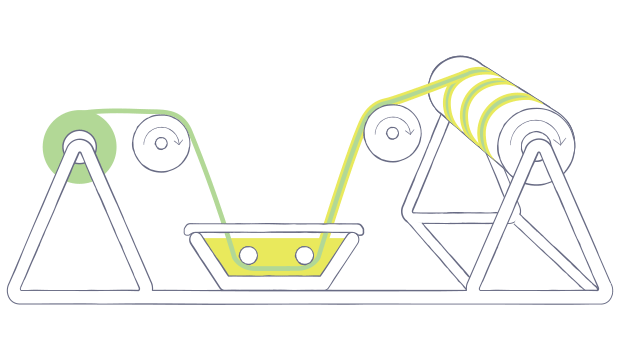
Process:
Continuous strand roving is fed through a resin bath and wound onto a rotating mandrel. The roving feed runs on a trolley that travels the length of the mandrel. The filament is laid down in a predetermined geometric pattern to provide maximum strength in the directions required. When sufficient layers have been applied, the laminate is cured on the mandrel. The molded part is then stripped from the mandrel. Equipment is available for filament winding on a continuous basis with to axis winding for pressure cylinders. Filament winding can be combined with the chopping process and is known as the hoop chop process.
Molds:
Filament winding uses mandrels of suitable size and shape, made of steel or aluminum, to form the inner surface of the hollow part. Some mandrels are collapsible to facilitate part removal.