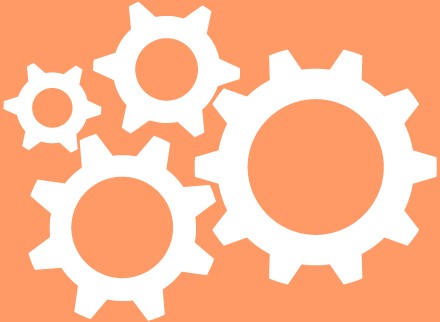
Closed Molding
In closed-molding, raw materials (fibers and resin) cure inside a two-sided mold or within a vacuum bag (shut off from air). Closed-molding processes are usually automated and require special equipment, so they’re mainly used in large plants that produce huge volumes of material—up to 500,000 parts a year.
Vacuum Bag Molding
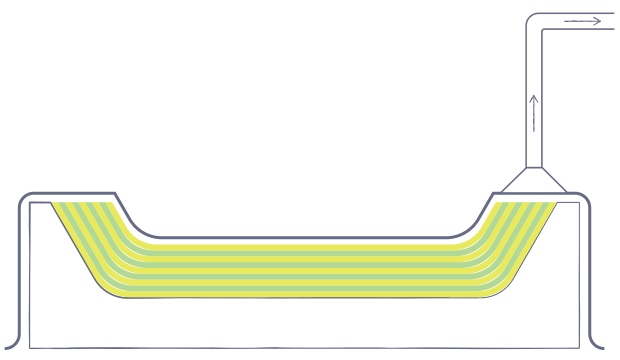
This manufacturing process is designed to improve the mechanical properties of laminate (two or more layers of fiber reinforcement bonded with a resin). A vacuum is created to force out trapped air and excess resin, compacting the laminate. High-fiber concentration provides better adhesion (between layers of sandwich construction). In addition, vacuum bag molding helps eliminate excess resin that builds up when structures are made using (open-molding) hand lay-up techniques.
Learn More
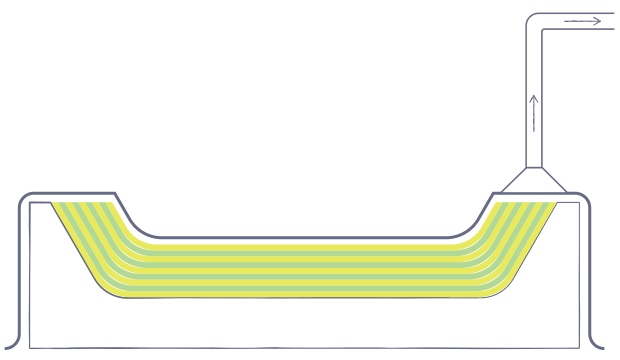
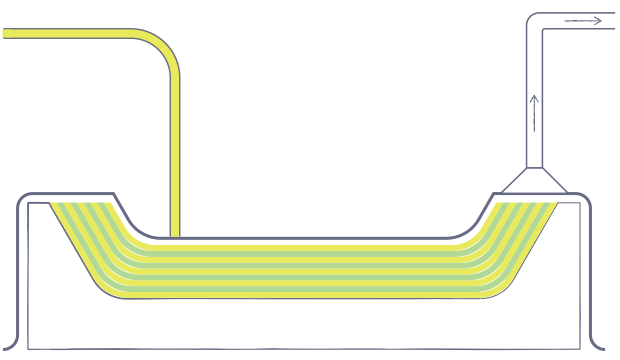
Vacuum Infusion Processing
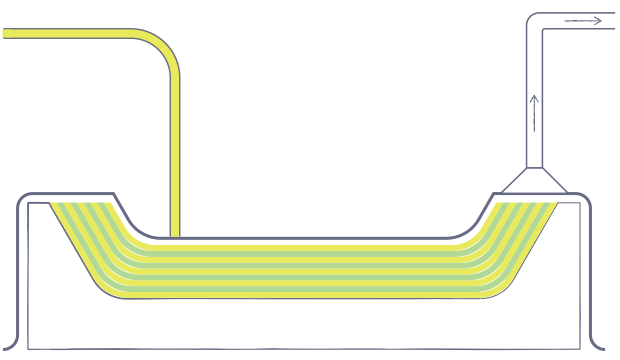
Vacuum infusion processing (VIP) is a technique that uses vacuum pressure to drive resin into a laminate. Vacuum infusion is typically used to manufacture very large structures. Vacuum infusion produces strong, lightweight laminates and offers substantial emissions reductions (compared to open-molding processing and wet lay-up vacuum bagging). This process uses the same low-cost tooling as open molding and requires minimal equipment.
Learn More
Resin Transfer Molding
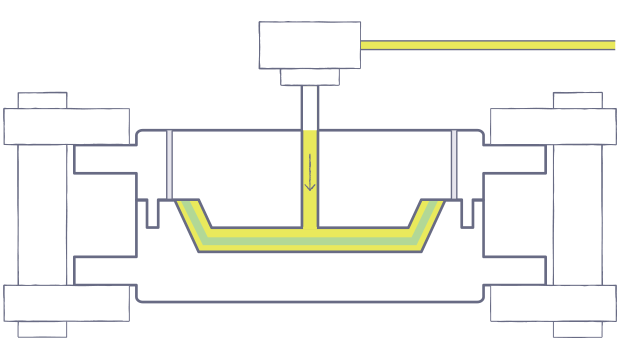
Resin transfer molding (RTM), sometimes called liquid molding, is a closed-molding method in which reinforcement material is loaded into a closed mold, the mold is clamped, and resin is pumped in (through injection ports) under pressure. This process produces complex parts with smooth finishes on all exposed surfaces. The process can be simple or highly automated–and cycle times are speedy. By laying up reinforcement material dry inside the mold, any combination of materials and orientation can be used, including 3-D reinforcements.
Learn More
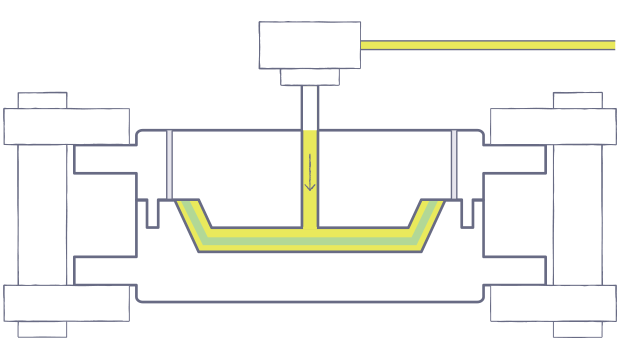
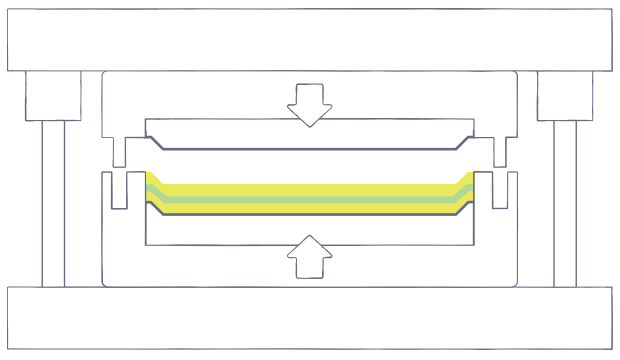
Compression Molding
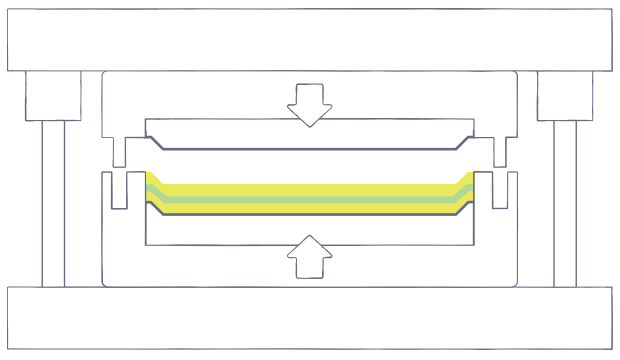
Compression molding is a manufacturing process in which composite materials are sandwiched between two matching molds under intense pressure and heat (from 250° to 400° F) until the part cures. This technique is used to rapidly cure large quantities of complex fiberglass-reinforced polymer parts. Compression molding features fast molding cycles and high part uniformity. The process can be automated. In addition, labor costs are low and it provides design flexibility and nice surface finishes.
Learn More
Pultrusion
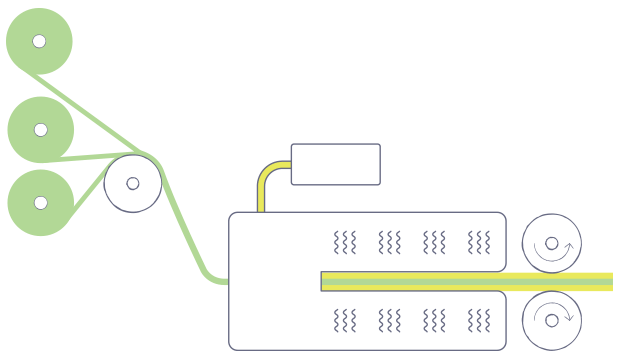
Pultrusion is used to form composites into long, consistent shapes like rods or bars. Continuous strands of reinforcement are pulled through a resin bath to saturate them, then pulled through heated steel molds that sculpt the composites into continuous lengths. The process operates continuously so it can be readily automated. Labor costs are low and finished products are very strong. Pultrusion is used to make products such as beams, channels, pipes, tubing, fishing rods and golf club shafts.
Learn More
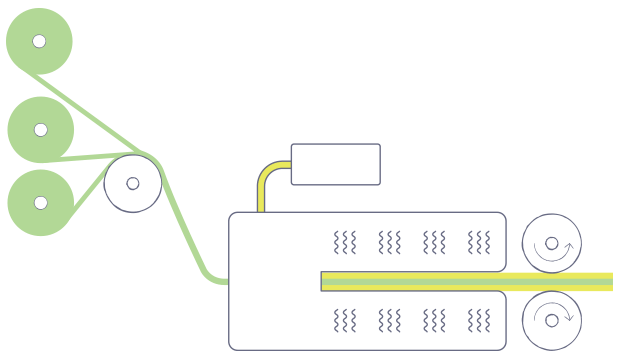
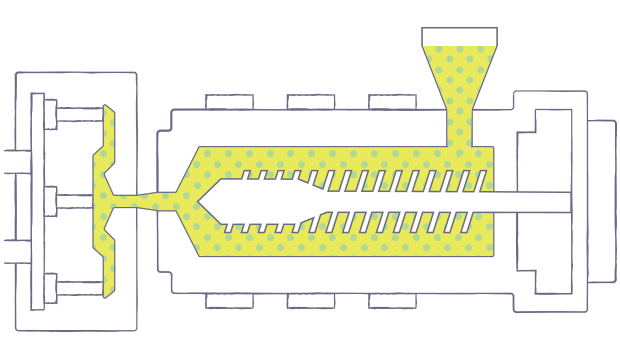
Reinforced Reaction Injection Molding
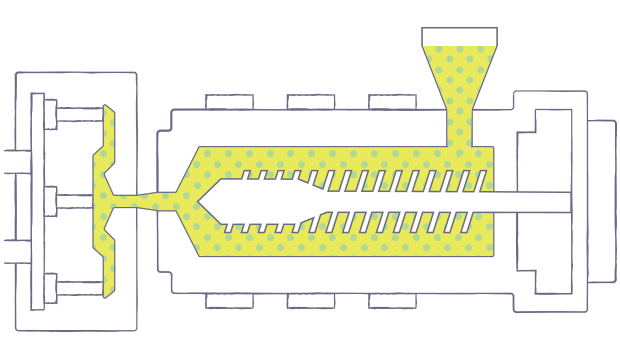
Reinforced reaction injection molding (RRIM) is widely used to make external and internal automotive parts. In this process, two (or more) resins are heated separately and combined with milled glass fibers. The mixture is injected into a mold under high pressure and compressed. The resin cures quickly. RRIM composites feature many processing advantages, including very fast cycle time, low labor, low mold-clamping pressure and low scrap rate. The RRIM process requires special resins and reinforcements.
Learn More
Centrifugal Casting
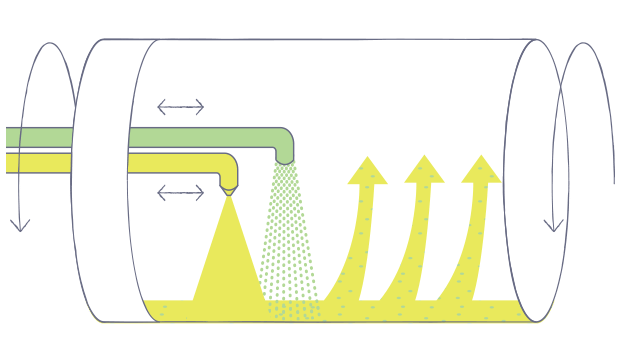
In centrifugal casting, reinforcements and resin are deposited against the inside surface of a rotating mold. Centrifugal force holds them in place until the material cures or hardens. Centrifugal casting is used to produce hollow parts (like pipes with two smooth surfaces). It’s especially well-suited for producing structures with large diameters, such as pipes for oil and chemical industry installations and chemical storage tanks. Centrifugal casting is increasingly being used to produce telephone, street light and other poles.
Learn More
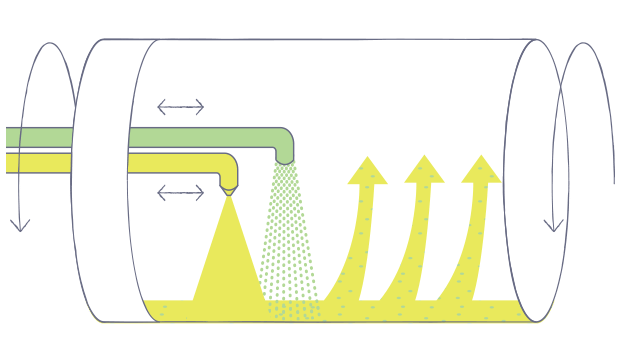
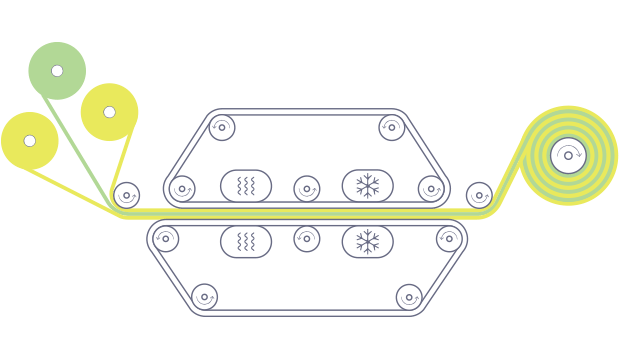
Continuous Lamination
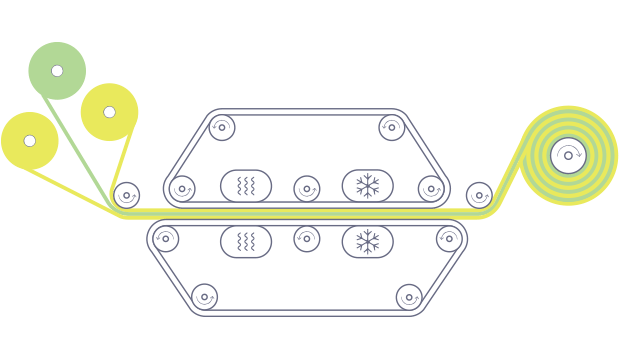
Continuous lamination is used to make flat or corrugated sheets and panels for products used in truck and RV sidewalls, road signs, skylights, building panels and electrical insulating materials. It’s a highly automated process in which fibers and resin are combined, sandwiched between two plastic carrier films—and guided through a conveyor process. Forming rollers shape the sheets, and the resin is cured (in an oven or heating zone) to form the composite panel. Panels are automatically trimmed to the desired width and length.