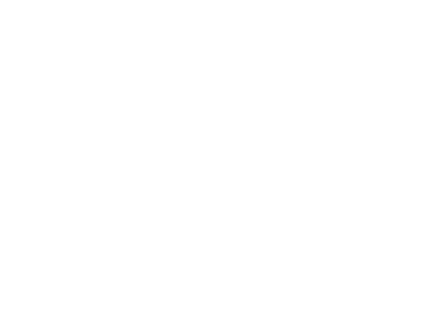
Surface Finishes
Used mostly for UV protection, corrosion resistance and aesthetics, surface finishes can be molded in process or secondarily applied coatings.
Surface finishes can be critical to the long-term appearances of composite products. FRP composites can accept a wide range of surface finishes, including gel coat, surface veils and adhesives. Other surface finishes include aliphatic isocynates, polyurethanes, polyesters, acrylics and epoxies and in some cases with fine sand added for additional protection.
- Gel Coat: A common surface finish for FRP composites is gel coat, a specifically formulated polyester resin that is applied to the mold surface prior to laminate build-up. It is designed to provide a cosmetic outer surface on a composite product and to provide weatherability for outdoor products. Gel coats are used to improve weathering, filter out ultraviolet radiation, add flame resistance, provide a thermal barrier, improve chemical resistance, improve abrasion resistance, and provide a moisture barrier. Gel coats are used to improve the product appearance such as the surface of a boat hull or golf cart. A unique benefit of gel coats is that they are supplied in many colors by the incorporation of pigments per the specification of the engineer.
- Surface Veils: In some composite designs, a surface veil is used to provide an improved corrosion or weather barrier to the product. A surface veil is a fabric made from nylon or polyester that acts as a very thin sponge that can absorb resin to 90% of its volume. This helps to retain an extra layer of protective resin on the surface of the product. Surface veils are used to improve the surface appearance and ensure the presence of a corrosion resistance barrier for typical composites products such as pipes, tanks and other chemical process equipment. Other benefits include increased resistance to abrasion, UV and other weathering forces. Veils may be used in conjunction with gel coats to provide reinforcement to the resin.
- Adhesives: Adhesives are used to attach composites to themselves as well as to other surfaces. Adhesive bonding is the method of choice for bonding thermoset composites and is sometimes used for thermoplastic composites. Adhesives should be used in a joint design where the maximum load is transferred into the component using the loading characteristics of the adhesive and the composites material. The most common adhesives are acrylics, epoxies, and urethanes. A high-strength bond with high-temperature resistance would indicate the use of an epoxy, whereas a moderate temperature resistance with good strength and rapid cure might use an acrylic. For applications where toughness is needed, urethane might be selected.
- Ultraviolet Protection: FRP materials by their nature are susceptible to ultraviolet (UV) degradation which usually begins with a cosmetic change in the color followed in time by potential chalking, peeling and cracking, eventually leading to a loss of resin on the material’s surface which is called fiber blooming. The rate of UV degradation is affected by geographical location, resin type, fiber loading and filler packages. FRP composites should be protected from UV by an opaque gel coat surface or by painting the exposed surfaces. Incorporating UV screens into the matrix is also useful. Of these techniques, gel coating is the most common because it provides good surface finish and a deep 10 to 20 mil (mm) thick protective surface.
- Painting: Painting systems are available for FRP composites finishes and are widely used in both the architectural and marine fields. Properly prepared FRP composites can also accept a wide variety of surface coatings, including oil- and water-based paint, as well as plural component systems such as urethanes. The non-absorbent, inert nature of FRP composites allow for surface paints to be applied. Paints need not be breathable and no extraordinary surface preparation is required beyond proper abrasion and removal of residual mold release agents. Ceramic tile, metal, wood, and other plastics can be adhered to FRP surfaces, provided differential thermal properties and panel deflections are allowed for either in the elasticity of the adhesive or mechanical attachment.