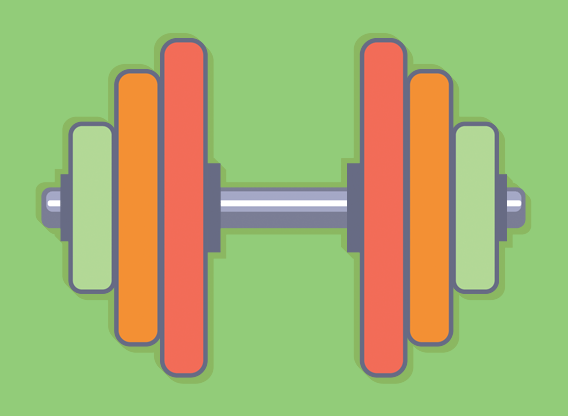
Strength
Composites are one of the strongest materials around. When you consider the density of the material, composites are much stronger than most other building materials. It’s no surprise they are the material of choice for everything from airplanes to automobiles.
By combining specific resins and reinforcements – and there are a lot of them – you can customize the formulation to meet specific strength requirements of any application. For example, you can alter the ratio of the resin and reinforcement or orient the fibers in one direction or various directions.
Composites are anisotropic, meaning the material properties change depending on the placement and number of layers of reinforcement materials – the fibers. This provides engineering flexibility so designers can tailor properties of the final product. When it comes to strength, there are four primary kinds that affect structural design: specific, tensile, shear and compressive strength.
Specific Strength
A material’s strength-to-weight ratio – also called its specific strength – is a comparison of its strength in relation to how much it weighs. The strength of a material divided by its density will give you the specific strength.
Engineers, designers and specifiers are increasingly seeking materials with a high specific strength. Some materials are very strong and heavy, such as steel. Other materials can be strong and light, such as bamboo poles. Composites can be designed to be both strong and light. Because they have very high strength-to-weight ratios, composites are a sought after material for applications where weight is paramount, such as airplanes and cars. Lighter vehicles use less fuel.
Tensile Strength
Tensile strength refers to the amount of stress a material can handle before it breaks, cracks, becomes deformed or otherwise fails. One measure of tensile strength is flexural strength – a material or structure’s ability to withstand bending. Tensile and flexural strength are important measurements for engineers and designers. Imagine building a bridge deck or a ceiling without knowing how much stress it could take before collapsing?
Tensile strength varies by material and is measured in megapascals (MPa). For example, the ultimate tensile strength of steel ranges from 400 to 690 MPa, while the ultimate strength of carbon fiber reinforced polymer composites ranges from 1,200 to 2,410 MPa, depending on fiber orientation and other design factors.
Shear Strength
Shear strength describes how well a material can resist strain when layers shift or slide. It’s important to know the maximum amount of shear stress (or force per unit area) a material can handle prior to failure. This lets engineers and designers know the amount of weight – or load – a structure can support and what may happen to the structure when forces are applied in different directions.
Shear strength in composites varies based on the formulation and design. Composites can be designed so shear stresses are oriented within a plane, transverse to the plane or throughout the layers (interlaminar). There are several ways to control shear properties, including fiber orientation, the sequencing of layers, the type and volume of fibers used, the type and density of core materials and more.
Compressive Strength
Compressive strength indicates how a material performs when it’s compressed or flattened by pressure. Some materials fracture or break when they hit their compressive strength limit, while others deform permanently.
Materials such as concrete and ceramics usually have a higher compressive strength, but lower tensile strength. Conversely, composites typically have higher tensile strengths than compressive strengths. Composites loaded in compression may buckle, kink or crush. That’s why it’s important to evaluate compressive loading for the specific fiber and resin combination chosen for an application and adjust the formulation accordingly.