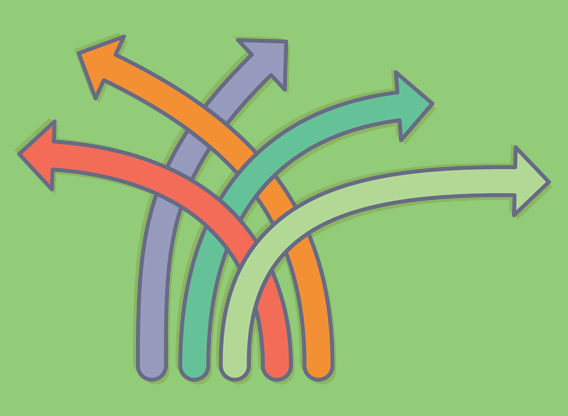
Design Flexibility
Composites pack a powerful one-two punch with their ability to be molded into complex shapes at a relatively low cost. This offers designers, engineers and architects a freedom not typically found with other competing materials.
Because composites are a blend of reinforcing fibers, resins and additives, they can be manufactured to meet an array of requirements. Designers are free to create exciting new products and, in many cases, are only limited by their imagination. Applications ranging from sports cars to wind blades take advantage of the inherent design flexibility of composites to produce complex shapes, add specific properties and enhance aesthetics.
Innovative Geometries
One of the biggest benefits of composites is the ability to mold them into complicated shapes more easily that most other materials. Intricate shapes and contours are possible without the need for high-pressure tools because composites are formed when the resin cures – or solidifies – during production. So composite parts can easily take on many shapes, whether they’re created in low volumes manually or manufactured using high-volume, automated processes.
Having options when it comes to the shape of parts and products is advantageous for nearly every industry that uses composites. Recreational boats have long been built with FRP composites because these materials can be easily molded into complex shapes, which improve boat design while lowering costs. More recently, high-profile buildings such as the San Francisco Museum of Modern Art have incorporated FRP cladding panels into their facades. None of the 700 undulating panels on the museum are alike, which makes for an eye-catching building.
Precise Properties
Designers like working with composites because parts can be tailor-made to have strength and stiffness in specific directions and areas. For instance, a composite part can be made to resist bending in one direction. The strategic placement of materials and orientation of fibers allows companies to design parts and products to meet unique property requirements.
Being able to address high stress and strain areas is critical in several markets, such as sports and recreation, where both high-end and everyday applications count on composites. At the elite level of competition, racing yachts in the biannual America’s Cup rely on exacting design of composite parts to carry structural loads throughout the yachts’ hulls and cross beams. By aligning fibers in various patterns laterally across skis, you can improve the torsional rigidity – the ski’s ability to resist twisting forces.
Surface Appearance
People are often drawn to composites because of aesthetics, with companies marketing the “carbon fiber look” on everything from phone covers to countertops. The popularity of the exposed weave appearance derives from the automotive industry, where high-end cars rely on carbon fiber-reinforced composites to not only enhance performance, but also reflect style. Options on the Aston Martin Vanquish, for example, include exposed carbon fiber roofs, door handles, wing mirrors and interiors.
But aesthetics aren’t reserved solely for luxury markets. Composite surfaces can be molded to simulate any finish or texture, from smooth to coarse. Consumers opt for composite countertops because they can be formed into any shape and customized into any color. Handles and knobs on household appliances look stylish and feel good to the touch. With composites, designers have endless options to create beautiful products.