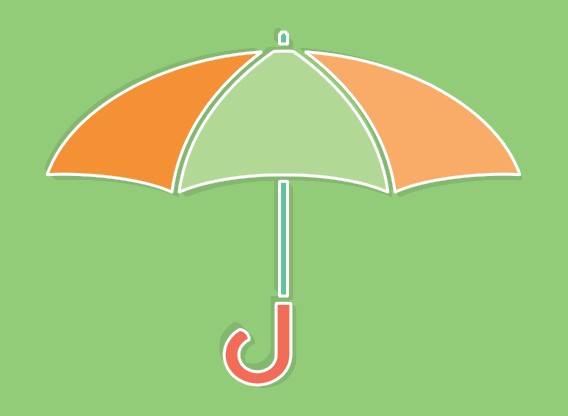
Corrosion Resistance
Products made from composites provide long-term resistance to severe chemical and temperature environments. Composites are often the material choice for outdoor exposure, chemical handling applications and other severe environments.
Composites do not rust or corrode. There are many examples of glass fiber reinforced polymer ductwork being in service in chemical manufacturing plants for more than 25 years, operating in harsh chemical environments 24 hours a day, seven days a week. Composites offer corrosion-resistant solutions for many industries, including air pollution control, chemical processing, desalination, food and beverage, mineral processing and mining, oil and gas, pulp and paper, solid waste landfill and water and wastewater treatment.
Corrosion resistance is determined by the choice of resin and reinforcement used within the composite application. There are various resin systems available which provide long-term resistance to nearly every chemical and temperature environment. The choice of reinforcements is much more limited but crucial for certain chemical environments. Properly designed composites have a long service life and minimum maintenance.
History of Corrosion Composites
In 1953, the first high-performance industrial corrosion resins were developed by Atlas Chemical and Hooker Chemical Companies. The pulp and paper and chemical processing industries were quick to recognize the benefits and use composites in their processing equipment.
In 1961, the Amoco Division of Standard Oil introduced the first underground gasoline storage tank. Between 1961 and 1965, Shell Oil and Owens Corning researched corrosion-resistant solutions, ultimately producing the first commercial line of large composite underground storage tanks.
During the 1970s, the use of composites in industrial applications became widespread. Then in 1989, the American Society of Mechanical Engineers published the seminal design standard for FRP tanks, Reinforced Thermoset Plastic Corrosion-Resistant Equipment. By the 1990s, the corrosion industry had accumulated 40 years of experience and case histories to build a positive performance record. Today, corrosion-resistant composites account for approximately 11 to 15 percent of the total composites market and generate an estimated $3 billion in annual sales.
Resin’s Role in Corrosion Resistance
One of the primary functions of resins in composites is to protect the fibers they surround. There are dozens of resins designed to provide corrosion resistance. Each unique formulation offers protection against specific conditions, such as caustic solutions, acidic environments, alkaline environments, oxidizing chemicals and high temperatures.
The first corrosion resins employed bisphenol fumurate and chlorendic anhydride resin chemistries. Subsequently, isophthalic resins were developed and became the mainstay of corrosion-resistant resins. Isophthalic resins – along with epoxy vinyl ester resins – are commonly used today.
Reinforcement’s Role in Corrosion Resistance
While the same resin matrix will typically be used throughout the composite structure, reinforcements may be used in three specific areas of the laminate. A fiberglass or synthetic veil is used at the inner surface of the laminate. The inner surface is the interface of the composite and corrosive material. The veil serves to provide a resin-rich (90% resin) surface for the composite while preventing micro-cracks in the resin which would otherwise occur if a resin-only surface (or gel coat) was attempted. The next layer is the chopped fiberglass layer which provides a more robust backup for the veil and is also resin-rich (70% resin). This layer is usually considerably thicker than the veil layer and when combined with the veil layer forms a 100 to 200 mil thick corrosion barrier. The last layer, and by far the thickest layer is the structural portion of the laminate. Different forms of fiberglass reinforcements can be used in this layer to provide a high glass content (35% resin, 65% reinforcement) structural layer: direct draw single-end rovings, fabrics, or choppable reinforcements.
There is a vast choice of materials used for the veil layer since this is the first line of defense against a corrosive assault. C-glass, E-CR glass, several types of synthetics thermoplastic non-wovens and carbon veil are the main material choices for veils. Each has a specific environment where they excel. E-glass is almost never used due to its poor corrosion performance. The material choices for the chopped fiberglass layer and the structural layer narrow considerably to E-glass and E-CR glass.
Industry Design Standards
If you’re planning a project using corrosion-resistant composites, the design will likely need to adhere to industry standards. The most widely used standards for corrosion applications are issued and maintained by ASTM International and the American Society of Mechanical Engineers (ASME). All standards address the basic issues of scope of applicability, design, materials, construction, quality control, testing and record keeping.
While there are more than a dozen standards associated with construction design related to composite corrosion applications, the primary one is ASTM C582. It’s a standard specification for contact-molded reinforced thermosetting plastic (RTP) laminates for corrosion-resistant equipment. It covers composition, thickness, fabrication procedures and physical property requirements for corrosion-resistant tanks, piping and equipment manufactured by contact molding – also known as open molding.